Screw conveyors come in many sizes, shapes and configurations and function in very similar ways. Knowing the basic terminology and the differences in each is a good first step to ensuring the screw conveyor you buy for your operation is the correct one. Below is a comprehensive list of the different types of screw conveyors and the functions of each.
Screw Conveyor
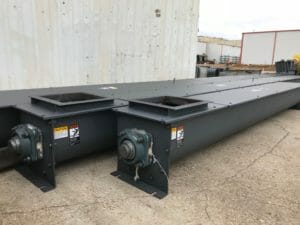
A screw conveyor is the most basic and widely used form. The term “screw conveyor” can be used generically to apply to all of these variations or technically to refer to one type. Technically, a screw conveyor is horizontal with a single control fed inlet, full pitch on the screw and a discharge. When we say control fed, we mean the screw conveyor is fed bulk material from another mechanical conveyor or feeder like a belt conveyor, rotary feeder, bucket elevator or screw conveyor. Screw conveyors are the easiest to design since the bulk material behaves very uniformly and there are many reference tables for sizing based on the material and required rate.
Screw Feeder
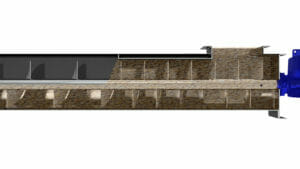
A screw feeder is horizontal with a single flood fed inlet, variable pitch or diameter and a discharge. Flood fed means the bulk material is flooded into the inlet from a bulk storage container like a hopper, silo or super sack. Special consideration must be made to the design of the flighting and drive to ensure the desired flow rate out of the storage container is achieved. Screw feeders use a shorter pitch through the inlet to meter the flow and then change pitch after the inlet to convey the bulk material. Screw feeders are very popular and an economical way to feed any bulk material.
Mass Flow Screw Feeder
A mass flow screw feeder is horizontal with an elongated flood fed inlet, multiple variable pitches or diameters and a discharge. The difference between the screw feeder and mass flow screw feeder is the length of the inlet. The longer inlet of the mass flow screw feeder means the flighting through the long inlet must be stepped up in capacity continually to allow the bulk material to flow evenly out of the bulk storage container. Mass flow screw feeders are used in very large bulk storage bins where the material can stagnant, adhere or rot if not evenly discharged.
Live Bottom Screw Feeder
A live bottom screw feeder is horizontal with a flood fed inlet, multiple variable pitch screws and a discharge. A live bottom screw feeder has multiple screws for very wide bulk storage discharges. The distinguishing factor here is the number of screws used in the feeder. A screw feeder or mass flow screw feeder will be no more than 2 screws side by side. A live bottom screw feeder will have more than two screws and maybe as many as 8. The challenge in designing a live bottom screw feeder is to not only make sure the screw flighting is designed to properly meter the bulk material but to make sure all the screws are rotating at the same speed. The speed is either controlled using a drive on each screw or by using spur gears or chain and sprocket to link the screws together. Live bottom screw feeders are used when a product is very bulky, nesting, and hard to move like wood chips.
Incline Screw Conveyor
An incline screw conveyor is a screw conveyor on an incline above 10deg and up to 45deg. As the screw conveyor gets steeper gravity continues to work harder against the product flow and the conveying efficiency of the flighting decreases. Special consideration must be made to the design of the flighting pitch, trough and speed to maintain the flow rate at the incline. A 9″ screw conveyor is 100% efficient at 0deg but only 10% efficient at 45deg. Incline screw conveyors are used in a number of applications where the bulk material needs to be elevated like to the top of a bin or bagging machine.
Incline Screw Feeder
Incline screw feeder is a screw conveyor on an incline above 10deg and up to 45deg. Like with an inclined screw conveyor, the efficiency of the flighting decreases as the incline increases. The required variable pitch to meter the bulk material only compounds the problems in an incline screw feeder because different pitches have different efficiencies as the angle increase. The design becomes very complicate when an inclined screw feeder has multiple pitches. It is best practice above 20deg to have a separate screw feeder to meter the flow and then screw conveyor to incline the product. Incline screw feeders are used to meter bulk materials out of bins and bulk bags to various process equipment like baggers or coating systems.
Vertical Screw Conveyor
A vertical screw conveyor is any screw conveyor over 45deg, but they are typically completely vertical. A vertical screw conveyor is very special and only works for granular products such as grain, plastic pellets, plastic regrind and similar sized bulk materials. Vertical screw conveyors rotate at 200RPM or more and require special inlet screw feeders to essentially prime the vertical screw conveyor. In applications where you need to elevate the bulk material and the product does not degrade in the high-speed screw a vertical screw conveyor is a great alternative to a bucket elevator. Vertical screw conveyors are used in the feed and grain industry, plastics manufacturers and recyclers and similar industries.
Thermal Screw Processor
A thermal screw processor is a generic term used for a screw conveyor where heat or cold is indirectly applied to the bulk material being conveyed. They can be as simple as a jacketed trough with steam flowing through it to keep a hot product hot or as complex as a hollow flight screw with cooling fluid flowing through it to cool down ash out of a coal fire boiler. A thermal screw processor is specifically designed for the application, flow rate and heat load required. A hollow flight thermal processor is the most compact indirect cooler technology available. Thermal screw processors are used in a wide variety of industries whenever bulk material temperature needs to be maintained or changed such as power plants, chemical processes, and even cutting-edge pyrolysis processes.
Shaftless Screw Conveyor
A shaftless screw conveyor is a screw conveyor with a single heavy spiral designed to convey the bulk material in a standard screw conveyor trough or housing. It can be horizontal, inclined and even vertical. Shaftless screws ride along a liner, usually UHMW, inside the trough. The spiral is much larger (1″-2″ thick) than a normal screw conveyor flight (1/8″ – 1/2″ thick) because the spiral alone must transmit all the torque from the motor and gearbox. To properly design a shaftless screw conveyor a detailed analysis of the spiral strength must be conducted to ensure a failure does not occur. Shaftless screw conveyors are used to convey sticky and moist bulk materials such as municipal wastewater and industrial sludge.